Leyland P76 Owners 2004 |
Technical problem |
|
Inlet Manifold Gaskets & sealing the leak.
- Written by "Mike Chadwick"
- Date: Tue, 30 Mar 2004
-
- From the time when I first owned a V8 P76 in October 1975, I have known them to be susceptible to this problem.
- A leaking inlet manifold gasket causes all sorts of running problems.
- I have detected it by using an atomiser to spray water onto the top of the inlet manifold while the engine is idling, and where there is a leak there is usually a hiss as the water is drawn into the motor, and it becomes easy to pinpoint the position of the leak as you observe the water disappearing into the inlet tract.
- There's no need to watch the exhaust emission, and water is usually less threatening than other fluids.
- I too have sealed an inlet manifold from the top with Sealastic or some other sealant, without having to immediately strip the manifold off.
- But this requires a 'long term' approach to manage properly.
- 1) I never throw out a used inlet manifold gasket if it is not irrepairably damaged.
- I remove as much of the old gasket material manually before using paint stripper, sometimes several applications before it is all cleaned off.
- I'm happy to learn of quicker ways of doing it, but it does work.
- Do it outdoors to prevent severe vapout inhalation, which may distress some people.
- The paint stripper can also be used to remove old gasket material from the head facing and the manifold flange facing.
- If I have a new unused inlet manifold gasket, I would not instal it unless I am certain that the gasket material is properly adhered to the metal gasket.
- I would strip off the fibrous material and use it bare, or put another application of fibrous material onto it. I have known severe internal manifold leaks where the engine has drawn crankcase fumes(with oil) straight into the affected cylinders, making carby adjustment impossible and making for one(at least) very oily cylinder.
- I do not rely on the clamping between the inlet manifold and the cylinder head to hold the gasket material in place on the metal gasket, because it will creep in service, causing the further leak.
- 2) I have successfully assembled the gasket without new gasket material being used, the best result being obtained using Loctite 518 or 515 anaerobic sealant - it only sets when air is excluded between the faces being joined together.
- To use Loctite successfully clearances must not be too big or it will soon, if not immediately, leak.
- I have used one or other of the Sealastics, but the main problem with that is the way that the excess squeezes out into the inside of the engine and into the inlet tracts and interfering with the gas flow.
- However while this is reasonably successful, I don't think it is the best way of doing it; I have known it to fail when after some use the Sealastic becomes soft after use, and allows the air/vapour into the inlet tracts.
- I certainly don't think it should be attempted before the inlet manifold has been checked and worked before assembly.
- 3) The inlet manifold casting itself should be examined for potential causes of leaks.
- I check for two characteristics which will impede a proper join between the inlet manifold and the cylinder heads, both characteristics caused by previous normal or excessive heat applications to the engine under running conditions over a prolonged period of time, nothing to do with original alloy blocks, etc.
- The first is that the flange edges will become a little proud, making the process of bolting the manifold down evenly an uncertainty, because the edges may prevent the manifold pulling down properly leaving internal and external possibilities for leaks.
- I remedy this by running a bastard file along the edges of the flanges and creating a 45 degree chamfer of about 1/16".
- This makes quite a difference to the way the manifold will pull down when assembled.
- The second is that the metal above the bolt holes along the flange 'moves' towards the cylinder heads because of the heat mentioned and the thickness of previously fitted inlet manifold gaskets, and subsequent re-tightening of the inlet manifold bolts after fitting new gaskets.
- This 'movement' (which is like a gentle hump) must be removed to regain a flat flange surface that will pull down properly against the flat cylinder head inlet flange.
- This can be done using a fine file and oilstone to finish, but I don't advise machining several thou off the whole flanges because this may render the inlet manifold unserviceable.
- Only metal above the bolt holes needs to be removed.
- These two tasks completed, the inlet manifold should bolt down evenly, with nothing on the flanges preventing that process. The other property that helps the manifold to pull down sqarely is the Loctite or other sealant that acts as a lubricant helping it to slide down into situ.
- Of course, the correct sequence for tightening should always be followed.
- Finally, using a hammer and a flat (steel) surface, hammer all the edges of the gasket and the holes until they are flat, eg around the holes in the gasket and along the edges.
- Be careful because some of these edges are sharp and will cut.
- Then if you have the inclination, I will explain a method which involves a lot of work, but has never failed for me.
- a) Take a used inlet manifold gasket, and clean it off thoroughly, as already described.
- b) Prepare the inlet manifold as already described in para.3 above.
- c) Purchase a sheet of gasket material (.4mm thick is my preference) and a Stanley knife if you don't possess one.
- You can buy larger sheets that will allow for gaskets of the size required at decent accessory shops.
- Another item you will need will be a small tin of Holden Sealing Compound 3835215.
- This stuff must be used where there is a positive draught and adequate ventilation, the vapour is not weak!! If you have no or little sense of smell, don't do this task on your own in a confined space.
- You will also need a cheap paint brush to apply this stuff evenly.
- Some thin cork gasket material may be useful for the ends of the valley if the rubber parts are too badly damaged to be used again.
- d) Cut two pieces of gasket material 6" x 18 3/8". Cut half way through the material along the 18 3/8" dimension and half way across the 6" dimension.
- Fold it down the half cut, and fold them over the flange edge. At this stage you can choose to cut out the waterway holes and the inlet tract holes and the bolt holes using the Stanley knife, or leave that task until last.
- I prefer the latter.
- e) Until you are practised, I suggest you do one side of the gasket at a time.
- Using the paint brush, apply the Holden Sealant to both sides of the flange area on one end of the metal gasket and to the side of the gasket material that will stick to the metal.
- Leave until tacky, then put the gasket material onto the metal gasket, folding it over and sticking it together with the sealant.
- Squeeze out any air, by putting 'x' cuts in all the holes with the Stanley knife if the holes have not been cut out.
- Using a roller of some description to squeeze the air out is a useful tip.
- To finally set it, put it on a flat surface and put a sheet of wood over the one side and let it set with books or something stacked on top of it.
- Setting overnight will be fine.
- Repeat the process on the other side next day, or whenever you are ready.
- f) Finally, when it is all set, cut out the holes (if it is not already done), which will not be difficult because the gasket material will be slightly dimpled where the holes are.
- You will have a very professional looking inlet manifold gasket that you know has the gasket material properly secured to the metal.
- g) Before assembly, check that the inlet manifold clamp seals are useable.
- If not, you can fabricate 1/16" thick cork substitutes with the Stanley knife and a ruler, and make sure that the little hole between the heads and the block are adequately filled.
- The Inlet manifold clamp may be 'rounder'than the casting at the end of the valley, meaning that the clamp seals
- are not clamped at the end of the clamp.
- Using a vice, the clamp can be squeezed out again until it clamps the seal right along its length - not
- difficult but a useful thing to do. Also, with the new inlet manifold gasket and inlet manifold dry, check their fit and bolt hole alignment. Then dismantle.
- g) On final assembly on the motor, having properly cleaned out the bolt holes in the cylinder head, paint both sides of the gasket material with sealant, and both the inlet manifold flanges and cylinder head flanges.
- Put the inlet manifold clamp seals(or whatever you're using) in situ, and put the inlet manifold gasket in situ, putting the clamps in place and the boltstightened down by hand to hold it all together.
- Place the inlet manifold in situ, and put in the bolts in the correct sequence as shown in the Workshop Manual, tightening up to 35 ft.lbs. in at least two, if not three passes.
- The manifold will pull down evenly putting an even pressure on all parts of the flanges.
- It is a good idea to let it set before starting the motor.
- Hopefully, you will be pleasantly surprised by its success. It will not leave ridges of sealant in the inlet tracts or in water passages, being the cause of blockages or restrictions.
- It will not leak.
- h) The only problem you will have with this method is when you want to remove it, because it will not move without the assistance of a (small) crow bar to break the seal.
- You may consider this a lot of work; it is. The result is excellent if properly done. If you are still using a WW Stromberg and you still have problems, fit an oversize butterfly spindle if you can get hold of one; that makes considerable difference to tuning and engine performance, as it reduces unwanted air intake at the butterfly.
- Good luck.
- Mike.
- Comments from others
- From: "minsai"
- Date: Tue, 30 Mar 2004
-
- Well Mike,'
- The only thing I can add to that, that I do, is use some Locktite 'Never Seize' on the manifold bolts.
- Why do the same job twice.
- It's not rocket science, it's attention to detail. As the old Rotary Club motto goes- DO IT ONCE- DO IT WELL.
- Thanks Mike for passing on the tools (knowledge ) to people to fix this problem.
- I hope people print it out,or Adrian puts it in the Technical section in the Club site.
- Regards Anton...
- minsai@bigpond.net.au
|
|
|
|
Last updated Jan, 2005 |
This web site may contain Copyright material
If you find any problems with the site, please email the
Web Editor 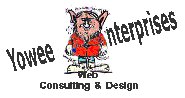 |
|