Leyland P76 Owners 2007 |
Technical |
|
Rust below the filler cap
Question
- From: James Mentiplay
- Monday, 5 March 2007
- Hi everyone,
- I remember reading somewhere about the possibility that the 1973 P76's didn't rust as badly around the filler cap like the 74 cars do.
- Could anyone who has any thoughts on this topic please tell why they think this is the case.
- Thanks in advance for any comments,
- James Mentiplay
Reply from Mick Clarke
- James I have got a reply from Martyn Hayes in the Vic club, and have attached his article from the club magazine on rust repair in this area (including photos) in the files section of the yahoo group.
- Mick.
- For your info:
- James,
- Mick Clarke sent me a copy of your forum question and asked me to give you a line on my theory about the rust around the filler cap.
- The earliest car in the Vic Club we have noticed with this problem is 11/73. If you have a look inside the boot (see article and photos in files section) you notice a sheet metal doubler panel on the left hand side around the filler.
- It appears that this panel is simply bonded and not spot welded to the inside of the quarter panel with the black sealant used prolifically around the all sheet metal joins.
- If you look inside the boot you will notice on rusted vehicles that the panel has clearly delaminated away from the quarter panel.
- If delamination occurs in conjunction with a leaking rear windscreen the water goes down into the space between them and rusts as the bonded surfaced are not primed in any way.
- It is my theory that due to accelerated demand for the car, corners were cut in production which in this case resulted in an inadequate bond between the two panels.
- I have four cars and the only one affected by rust under the filler is 03/74.
- The other three 05/73, 07/73,10/73, have no problem with rust.
- Of the last two mentioned one sat in storage for 20 years or more (Last Reg 1983) in coastal sea air and the other in a 20 years in an open paddock.
- The one that is rusty under the filler I acquired from the original elderly owner and this car was fairly well looked after.
- This leads me to theorise that the problem is one of manufacturing technique which I believe was modified around the end of 1973 (to our detriment) when the pressure was on.
- I wrote an article outlining my repair and placed it in our club magazine (March 06).
- I stand by my conviction that if ever the bastard rusts again I’ll bare my butt in Burke St (the main street for those in WA who never heard of it).
- I have attached a soft copy to attach to the email.
- Regards
- Martyn
Article from the Victorian Club
Repair of Rear RH Quarter Panel – Petrol Filler Rust
- Upon removing the rear window on my Bitter Apricot Six, I discovered that the only thing holding it on was the chrome strip.
- This of course explains the rust in the boot and around the petrol filler.
- Club Scientist/PHD and Parts Tech mogul, Marcus Kneebone, has concluded that the Petrol Filler rust is the scourge of cars built predominantly in 1974, although the theory came unstuck with just one exception and that was Michael McKenzie’s Bold as Brass 11/73.
- It appears that the major cause is water getting between the doubler plate and the panel skin.
- Problems can be prevented if you check that the plate has not delaminated and if so treat with fish oil and try to reseal the mating surfaces. Obviously keeping the water out in the first place by maintaining a good rear windscreen seal and rust free structure around it will certainly also help prevent problems.
- If you already have a rusted bubbling outer skin around the filler, the only way to fix it without the problem reoccurring is to get all of the rust out, particularly from between the double plate and the panel.
- In thinking about the fuel filler rust problem and that other members have had the experience of rust returning after previously attempting to repair it, I though it was time to try something different.
- I guess there are several ways to approach this repair but this story is about how I did it My background as an Aircraft Maintenance Engineer certainly helped as you will pick up from reading on.
- Firstly I peeled back the doubler plate on the inside and cleaned and treated the rust between the surfaces.
- I cut the rusted section of the outer skin and made up an insertion patch from new metal slightly thinner than the panel skin that will allow the application of a thin coat of filler after assembly to obtain a flush finished surface.
- I drilled through both the outer skin and the doubler a pattern of holes.
- The holes are then countersunk on the inside to receive a flush head solid rivet.
- After preparation and deburing the flaying surfaces were coated with a liberal amount of aircraft fuel tank sealant (Commonly known as “goop”) and solid riveted with the aid of a pneumatic hammer and dolly.
- Note that this operation is a two person job, one on the gun one on the dolly.
- You need also to ensure that the two surfaces are tightly clamped to exclude gaps and expansion of the rivets in-between the surfaces.
- The sealant should squeeze out as you gun up the surfaces ensuring a good bond with no air between the surfaces.
- (It is my view that a much better finish can be obtained than by welding as there is no heat generated that can distort the metal, and you do not burn away the protective coatings).
- The insertion patch is also riveted in place with goop.
- If its good enough for a B747 its good enough for a P76.
- Where no access to both sides exists then countersunk blind rivets must be used however, it is recommend getting good quality steel or titanium rivets in order to obtain good tensile pull up of the surfaces.
- The job is then finished on the outside with a coat of fibre reinforced putty followed by finishing coats of plastic putty (Bog) to obtain a smooth finish.
- The inside surfaces are then coated with aircraft fuel tank sealant to obtain a neat job and to ensure water is excluded from entering between the surfaces.
- I am now confident the make the statement that “If it ever rust again I will bare my Butt in Bourke Street”
- Famous last words -
- Martyn Hayes
|
|
|
|
Last updated March, 2007 |
This web site may contain Copyright material
If you find any problems with the site, please email the
Web Editor 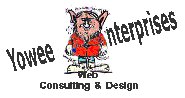 |
|